WELDING MACHINE SET TESTING
OXY/FUEL GAS SET TESTING
Welding Safety
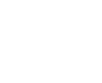







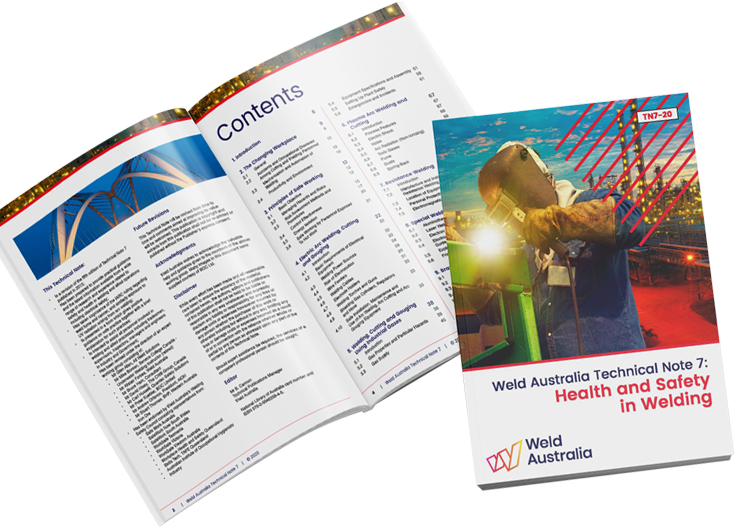
Welding Safety Allied Processes References
AS 1674.2 - 2007 Safety in Welding + Allied Process - Electrical
WTIA - Tech Note 22 - Welding Electrical Safety
WTIA - Tech Note 7 - Health & Safety in Welding
Expert Technicians
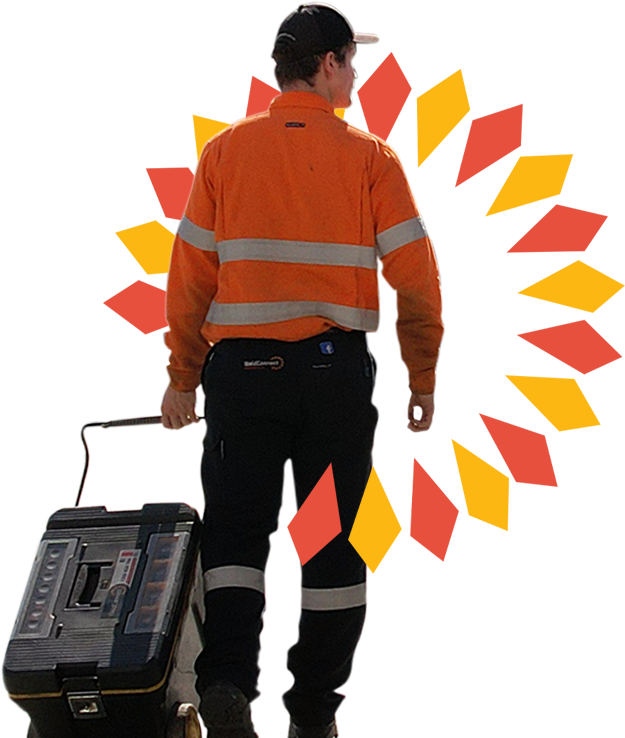
Safe/Welding
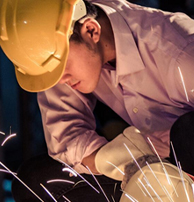
Hazard
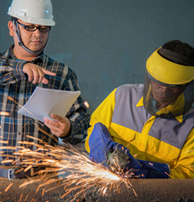
Risk

Control
WeldConnect operates a Quality Management System
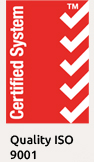
OXY FUEL INSPECTIONS
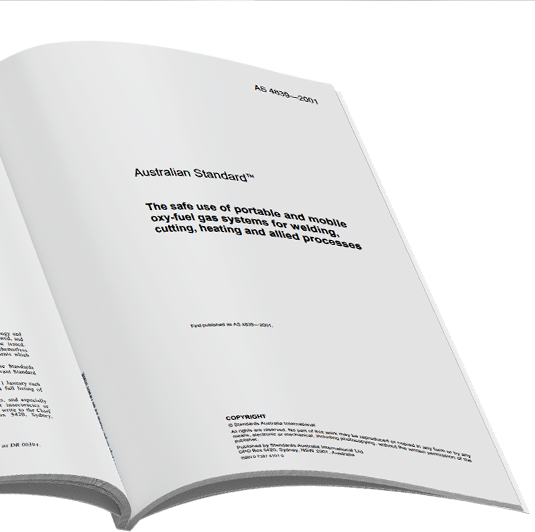
Guidance for you
Referenced Documents:
4839-2001 - The safe use of portable and mobile oxy-fuel gas systems for welding, cutting, heating and allied processes
4332 - 1995 - The storage and handling of gases in cylinders.
4603 - 1999 - Flashback arrestors - Safety devices for use with fuel gases and oxygen or compressed air.
4289 - 1995 - Oxygen and acetylene gas reticulated system.
1335 - 1995 - Hoses and hose assemblies for welding, cutting, and allied processes.
4267 - 1995 - Pressure regulators for use with industrial compressed gas cylinders.
Further references are documented in WeldConnect Acts, Regulations and Australian Standard file.
Safe Work Australia - Model Code of Practice - 25 May 2018
Oxy Fuel Gas Inspections
As 4839 Maintenance Guide
Equipment | Weekly (if in constant use) or before every use (to be per-formed by the operator) | As nominated (to be carried out by a technically competent person) | Refurbishment or replacement intervals (equipment condition determines whether refurbishment or replacement is required.) |
---|---|---|---|
1. Regulators (including their integral protective devices) | According to the manufacturer's instructions including — visual examination to determine suitability for service (e.g. gas, pressure rating, damage); condition of threads and sealing surfaces; and oil or grease contamination. Leak test all joints at working pressure. | Six monthly: Functional tests to ensure the correct operation of internal components | Manufacturer or supplier recommendation, but not exceeding five years.* |
2. Flashback arrestors and other external devices (including non-return valves) | Visual examination to determine suitability for service (e.g. gas, pressure rating, damage); condition of threads and sealing surfaces; and oil or grease contamination. Leak test all joints at working pressure. | Yearly as detailed in AS 4603 or following a flashback: Proper functioning of the non-return valves and flashback arrestors. For pressure-activated valves, check there is no flow in the normal direction with the valve tripped. | Manufacturer or supplier recommendation, but not exceeding five years.* |
3. Hose assemblies | Visual examination to determine suitability for service (e.g. gas, pressure rating, damage); condition of cover; and threads and sealing surfaces of the end fttings. Leak test all joints at working pressure. | Six monthly: Check for absence of cuts and excessive wear by bending the hose in a tight radius, to ensure reinforcement is not visible | Determined by the hose assembly condition. |
4. Blowpipes, mixers and at-tachments | Visual examination for damage of the threads and sealing surfaces of the hose connections and the attachment connections. Leak test all joints at working pressure. | Six monthly: Test control valve function. Blank the attachment connection and leak test for internamal-function. | Manufacturer or supplier recommendation, but not exceeding five years.* |
* Regulator elastomers and seals will wear and deteriorate in service and deteriorate out of service. Items stored for one year or over without use should receive inspection as per the annual maintenance inspection